Forming Heat Exchangers With Pulsed Electrochemical Machining (PECM)
- Sara Hagmann
- Apr 30, 2021
- 4 min read
Updated: Jan 18, 2024
The heat exchanger industry is an enormous field, with a wide variety of applications. The market can be divided in many ways; however, the focus of this article is on high heat flux applications, commonly served by heat exchangers with liquid or phase change materials as their working fluid.
Questions on ECM applications? Contact us anytime.
Despite the diversity in end applications, the essentials of form and function remain the same, whether you have aerospace engines, microprocessor cooling, or catalysis reactions in mind. These essentials include several common issues in manufacturing heat exchangers for optimal efficiency.
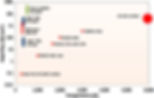
Comparative heat flux for a variety of applications. Source: PNNL
Much of a heat exchanger’s efficiency correlates to the quantity of surface area and the length of the path that the fluid travels through the system. High aspect ratios, thin walls, and tight spacing can all increase the heat exchanger's efficiency, but such complex geometries can be difficult to achieve, especially in materials compatible with high temperature applications. Fortunately, PECM, or pulsed electrochemical machining, is especially well-suited to creating these kinds of shapes – even in typically hard-to-machine materials.

High aspect features in an IBM thermal conduction module. Source: IBM
THIN WALLS
Using thin walls in a heat exchanger makes it easier to transfer heat between hot and cold regions, boosting the heat exchanger’s overall efficiency. However, many manufacturing processes rely on thermal or contact techniques for forming wall features, which can cause thin-walled channels to deform. These deformations can lead to a few potential issues including irregular channel sizes (resulting in un-even heat flow), interference with a mating component, or a lack of effective bonding in a brazed configuration.
In contrast, Voxel’s electrochemical machining process is both non-contact and non-thermal, eliminating the risk of these deformations. PECM does not compromise the material’s intended shape, also preserving its ability to mate or interface with other parts during assembly.

Rocket engine combustion chamber with cooling channels. Source: Kostas Makris
DURABLE MATERIALS
Material choice can have a critical influence on the overall heat exchanger efficiency. Design engineers are faced with a complex material optimization decision between thermal resistivity, matching the coefficient of expansion, bonding or joining concerns, corrosion, system mass, and cost.
Many low temperature applications utilize aluminum alloys due to its machinability and formability, low cost, low weight, and high thermal conductivity. However, higher heat flux or higher temperature applications often require more advanced material choices.
For example, high temperature rocket engine or printed circuit heat exchangers often need to manage corrosion and temperature issues that may require stainless steels or nickel super alloys. In chip-level cooling, it may be important to match the thermal expansion of silicon, requiring a metal matrix composite (e.g. AlSiC) or a refractory metal.

Relationship between thermal expansion and thermal conductivity for a wide variety of materials. Source
While ceramics, like silicon carbide, are an ideal theoretical solution given their high thermal conductivity and resistance to corrosion, they are generally difficult to bond and also brittle, which can make implementation difficult for many applications. Fortunately, material researchers are continuing to develop novel metallic alloys, such as high-entropy alloys, which are durable, temperature resistant, and can be bonded or brazed. 5
Voxel has experience using PECM on a wide array of metallic materials relevant to heat exchangers including copper alloys, nickel super alloys, and metal matrix composites.
HIGHER DENSITY COOLING FEATURES
Increasing the quantity of cooling features per unit volume can be achieved by decreasing spacing between features, reducing the size of each feature, or both. These changes increase the volumetric surface area, thereby improving the heat transfer capability. This can be particularly valuable when there are strict packaging requirements. Increased cooling feature density can reduce the overall size and enable the heat exchanger to be located closer to the heat source, thereby improving efficiency. In addition, a heat exchanger with improved volumetric efficiency can reduce the quantity of materials required – particularly important for high-value (i.e. expensive) materials or industrial applications like printed circuit heat exchangers (PCHE) where the scale of the installation leads to high material costs.
This “densification” of the critical heat exchanger features can be challenging to achieve through conventional manufacturing methods – particularly when the channels have an aspect ratio greater than 1:1. For a forming or cutting processes, this may require smaller, more delicate forming tools which could exceed the process capabilities. An additive technique may struggle to achieve the thin-wall requirements due to thermal distortions. Fortunately, unconventional manufacturing processes like PECM can be particularly effective at creating high density cooling features.

Inconel 625 high temperature heat exchanger, manufactured by Voxel using electrochemical machining. Source: Voxel Innovations
PARALLEL PRODUCTION
At the end of the day, cost is one of the most critical concerns for heat exchangers – especially those used in high quantities. The above sections describe many ways that the system-level or operational costs can be improved; however, those must be balanced with the device cost. One of the core strengths of PECM is the ability to machine multiple features in parallel. Instead of creating one slot at a time, we can create 10s or 100s of slots at a time. In this way, we can dramatically increase the process throughput of heat exchangers with high feature count. Parallel production enables faster production, which in turn yields a significantly lower cost per part, although the exact savings depends on the part and other variables.
In conclusion, pulsed electrochemical machining is highly suited to heat exchanger manufacturing, given its ability to create thin walls, shape typically hard-to-machine materials, preserve narrow spaces between features, and produce many features or parts simultaneously. If you are interested in learning more about using PECM for your heat exchanger, contact us with any questions.
There are a multitude of other ECM applications to explore-- consider reading our other articles detailing these specific applications for the technology.