Photochemical Etching vs. Electrochemical Machining
- Sara Hagmann
- Mar 8, 2021
- 4 min read
Updated: Feb 12
One of the primary disadvantages of conventional machining methods, such as CNC milling or electric discharge machining (EDM), is the impact of mechanical and/or thermal stress on the part to be machined. Other options exist, but they are less well-known and can be easy to confuse. Here, we offer a comparison of two of these unconventional options, namely photochemical etching and electrochemical machining (ECM) or pulsed electrochemical machining (PECM).
Photochemical Etching
Photochemical etching (PCE) is also known as chemical etching or chem etch. This process begins with a cleaned sheet of metal coated with a light-sensitive material called photoresist. This coated metal is sandwiched between photomasks (or just one, if the desired result is only etched on one side). Photomasks (or photo-tools) are negative images of the desired part, with clear and opaque areas.
High energy UV light is applied to the coated metal and photomasks, which cures the photoresist where the masking was transparent, and leaves it uncured where the masking was opaque.
Next, an acidic etchant removes material left unprotected by the photoresist. While cured photoresist is unaffected by the etchant, other chemicals easily remove uncured areas, providing access to the metal for dissolution by the acidic etchant. The metal is soaked or sprayed with the etchant to remove the metal in an isotropic fashion, creating the desired features. Finally, the remaining cured photoresist is removed mechanically or chemical to reveal the final part.
Electrochemical Machining

In electrochemical machining, a custom tool electrode (or cathode) is created in the inverse geometry of the desired part. This tool is placed next to the unshaped metal (or anode) with a miniscule gap in between.
While a current is applied, an electrolyte solution is pumped into the gap. The current dissolves the metal, atom by atom, into the desired shape while the electrolyte simultaneously washes away waste material. The desired shape is created based on the proximity, and therefore local current density, created between the tool electrode and workpiece. Areas with a small gap dissolve quickly while areas with a large gap dissolve slowly or not at all.
Similarities
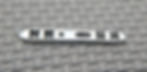
These processes are alike in that neither generate mechanical or thermal stresses. This means that burrs, HAZs, and tool wear are not a factor. Furthermore, both processes are chemically driven and can machine many metals or alloys regardless of the metal’s hardness, even heat- and wear-resistant refractory metals. Even in these tough metals, both PCE and ECM are suited to high volumes of high quality features.
Differences
Unlike ECM, however, PCE is best suited to sheet metal. For one, PCE generally can’t cut very deeply and is limited to cuts of a 1:1 aspect ratio due to its isotropic behavior, i.e. it dissolves metal in all directions at roughly the same speed. This limits PCE to generally semicircular channel shapes of the same depth (unless multiple masking operations are used) or to through-etching. Additionally, the flat material allows it to be automated, whereas if it was used on a curved surface, the process changes significantly and becomes more expensive. This does mean, however, that photochemical machining is well-suited to cutting out thin, 2D parts or etching shallow channels or textures on a surface.
In contrast, ECM can produce high anisotropic features driven by the shape of the electrode. This means channels can be square, trapezoidal, or freeform and depths of features can vary continuously across the part while using a single tool. The aspect ratio is also not a significant limitation, with the ability to create thin walls with >20:1 aspect ratios. In addition, this allows ECM/PECM to create parts which are fully 3D from either flat or contoured workpieces.
The photomask “tooling” used in PCE is inexpensive, which lowers upfront cost and delivery time. In contrast, ECM/PECM requires the creation of a metal electrode tool which, although non-sacrificial, does cost more up front in non-recurring engineering (NRE) expenses.
This tool difference leads to accuracy differences between the two processes. Photomasks can move or distort, especially on large surface, decreasing this process’s repeatability and overall accuracy. Accuracy values are often quoted as +/- 10% of the feature depth which, for a deeper cut or feature, can become significant. ECM and PECM, on the other hand, can achieve repeatability in the <10um range as the electrode shape does not change over time, providing a differentiator over chemical etching, especially for deeper features.
Applications
Put simply, if the completed part is a large, flat piece of textured metal, or even sheet metal with an array series of shallow features or cuts, PCE is the better choice. In addition, if low volumes and low up-front costs are required, PCE will be more economical. That is not to say that this kind of shape could not be produced with ECM/PECM, but rather that PCE has a significantly lower price point, making it more practical.
On the other hand, if the part has varying feature depths or 3D geometry, or requires higher aspect ratios and very low tolerances, ECM/PECM is well suited to the task. This is especially true for high-value and/or high-volume orders.
If you would like to learn more about how ECM can help to meet your manufacturing needs, reach out to us via our contact page or at info@voxelinnovations.com. We're ready to help.
---
This article is part of our ongoing “PECM vs. Competing Processes” series that compares PECM to other machining processes.